Under the unified scheduling of the factory’s “brain”, robotic equipment and intelligent logistics systems work together in an orderly, efficient, and stable manner, achieving intelligent production, intelligent logistics, and intelligent management.
Recently, in collaboration with a globally recognized 5G technology provider and a well-known Thai telecommunications operator, SIASUN successfully constructed the first 5G smart factory in the SFT Industrial Park, which is a renowned automotive parts supplier located in the industrial and economic zone on the east coast of Thailand in Southeast Asia. This smart factory is now officially in operation.
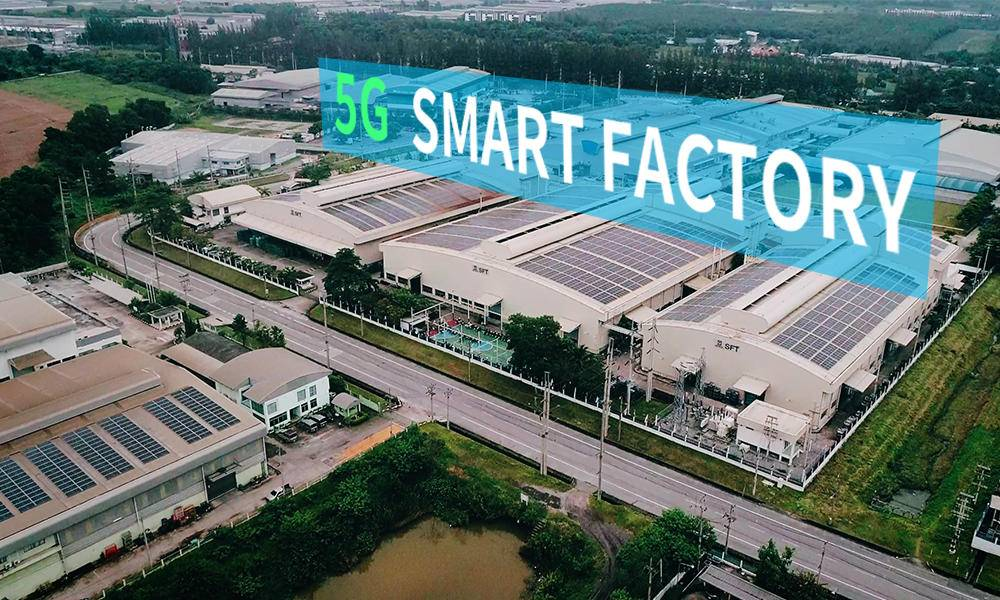
Traditional production workshops in Southeast Asia often have materials stacked haphazardly, and material handling is typically carried out through a combination of manual labor and forklifts. The presence of collisions and other safety risks between forklifts and personnel hinders the improvement of production and logistics efficiency. The innovative 5G smart factory effectively addresses this issue. In the complex factory environment, the agile SIASUN Automated Guided Vehicle (AGV) robots, equipped with SIASUN’s self-developed laser navigation and intelligent perception technology, can automatically identify surrounding personnel and various production equipment, realizing autonomous avoidance and path planning. Furthermore, these robots can navigate smoothly through narrow aisles, accurately reach various target locations, dynamically identify target pallets in real-time, and establish efficient connections between the stereoscopic warehouse, robot workstations, loading and unloading points on the production line, and raw material receiving points. As a result, the logistics operation efficiency in the factory is significantly enhanced.
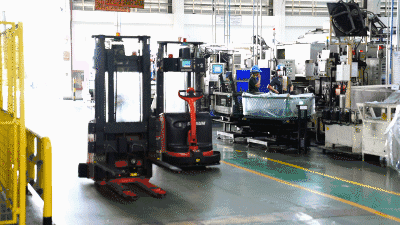
At one side of the smart factory, the SIASUN-built robot loading station is in motion. SIASUN integrates robots with 3D vision technology, enabling them to flexibly grasp materials that are in a disordered state and complete the automatic loading process. This not only improves production efficiency but also enables automatic statistics gathering and system error prevention, further enhancing the intelligence level on the production line.
This project has garnered high attention and recognition from the Thailand’s Ministry of Digital Economy and has attracted numerous business delegations from various Southeast Asian countries for visits and investigations. It sets a benchmark for the construction of modern smart factories in Thailand and even in Southeast Asia, injecting new impetus into China’s ongoing efforts to promote the high-quality development of the Belt and Road Initiative.